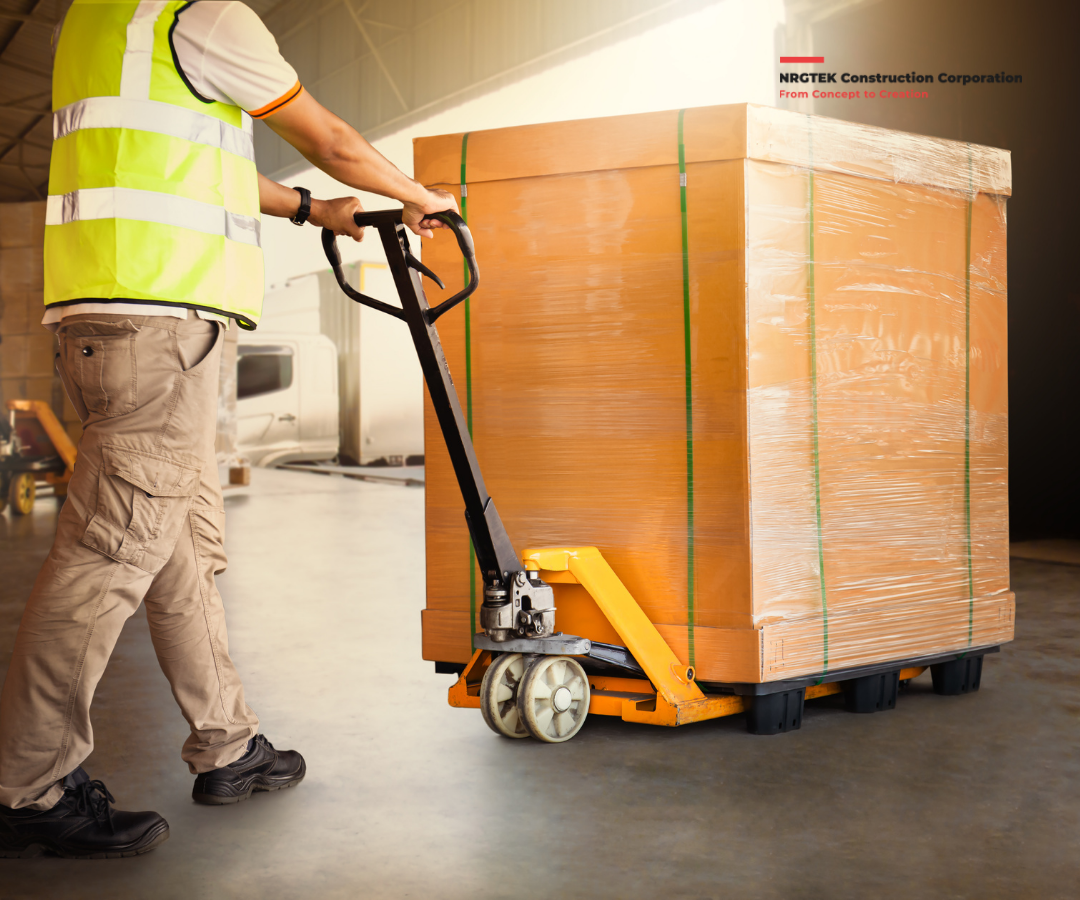
Although difficulties have always existed in British Columbia’s (BC) construction sector, supply chain interruptions in recent years have made project management even more difficult. The challenges have been numerous and include labor shortages, lengthy shipment delays, and growing material costs. We have direct experience with the effects of these disruptions on schedules, budgets, and project delivery as a company working in BC’s vibrant construction industry. However, we and many others in the business are effectively navigating these hurdles because to innovation, adaptation, and strategic planning.
In this blog, we’ll explore the current supply chain issues facing BC’s construction industry and share how our company is adapting to ensure that projects are completed on time and to the highest standard.
The Supply Chain Challenges Facing BC’s Construction Industry
1. Material Shortages and Price Increases
The COVID-19 pandemic’s worldwide disruptions are still having an impact on the building sector. There were shortages of necessary goods including steel, concrete, lumber, and other building supplies as a result of supply systems’ inability to keep up with the spike in demand for construction materials. Accurately estimating project expenses became challenging due to the sharp increase in lumber prices in particular. Material shortages continue to result in major delays and budget adjustments even as prices have begun to level out.
2. Shipping and Transportation Delays
Delivery delays of essential supplies and machinery have been caused by port congestion, shipping backlogs, and a lack of truck drivers. Construction companies are experiencing longer lead times for materials due to the large number of shipments that are backed up at ports or on the road. This forces us to modify project timelines and occasionally look for alternate delivery routes.
3. Labor Shortages
The lack of competent workers is another urgent problem facing BC’s building sector. It has been challenging to get new talent into the crafts as many workers have retired or relocated to other industries. Project schedules and costs have become even more complicated as a result of the mismatch between the available workforce and the demand for qualified labor.
4. Inflation and Volatile Pricing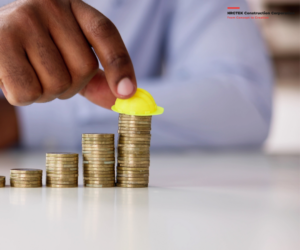
The volatility in global markets, combined with fluctuating fuel and labor costs, has made it difficult to predict costs accurately. Construction projects require meticulous budgeting, but price increases in materials and labor can lead to cost overruns. For contractors, this creates uncertainty that can impact cash flow and long-term project planning.
How Our Company Is Adapting to Ensure Timely Project Completion
Despite these challenges, our company is committed to finding innovative solutions and maintaining the highest level of service for our clients. Here are the key strategies we are employing to ensure that projects are completed on time, within budget, and with the quality that BC’s construction industry is known for:
1. Building Stronger Relationships with Suppliers
Developing closer ties with our suppliers is one of the best strategies we have for reducing supply chain problems. In order to prioritize our projects and guarantee a consistent supply of supplies, we are collaborating more closely with reliable local vendors. We can improve communication, make more precise plans, and prevent last-minute shortages by establishing these solid partnerships.
In order to lessen reliance on any one source, we have also diversified our supply chain to include both domestic and foreign vendors. This enables us to get products with greater flexibility in the event that one supplier has shortages or delays.
2. Proactive Project Planning and Scheduling
Being ahead of delays requires anticipating possible supply chain disruptions. As a result, our project managers are collaborating closely with manufacturers, suppliers, and logistics partners to obtain up-to-date information on delivery schedules and material availability. We may reschedule deliveries, modify project timelines in advance, and deploy resources in a way that has the least possible impact by obtaining comprehensive information early on.
If an essential part is delayed, for instance, we will reschedule building to focus on activities that don’t require it, or if there are substitute materials available, we might switch to using them. This proactive strategy lessens the overall impact on project timeframes and helps us keep up momentum on building sites.
3. Investing in Technology for Better Visibility
To navigate these challenges more efficiently, we’ve adopted advanced project management and supply chain management software. These tools allow us to track materials and deliveries in real- time, providing a clearer picture of potential delays and enabling us to make adjustments as needed.
Additionally, we’re using Building Information Modeling (BIM) to enhance collaboration between our teams, subcontractors, and suppliers. BIM enables us to visualize the entire project digitally, making it easier to identify and resolve potential issues before they cause delays. Technology also helps us better manage the procurement process by enabling more accurate forecasting. We can predict future material needs more precisely, which allows us to order materials in advance and avoid last-minute rushes to secure supplies.
4. Exploring Alternative Building Materials
We’re looking into substitute building materials that might provide comparable quality at a lesser cost or be more easily accessible in light of material shortages and price rises. For instance, utilizing modular components or engineered wood products might expedite the building process and lessen dependency on conventional lumber supply.
Additionally, we are collaborating with designers and architects to incorporate locally produced and sustainable materials into our projects. This not only relieves pressure on the supply chain but also satisfies BC’s rising demand for environmentally friendly building techniques.
5. Focus on Workforce Training and Retention
We have concentrated on recruiting and keeping skilled individuals in light of the labor difficulties in BC’s construction sector. To assist in educating the upcoming generation of construction workers, we have teamed up with nearby trade schools and apprenticeship programs. In order to keep our talented staff, we have also implemented incentives including competitive pay, chances for additional education, and a dedication to workplace safety.
We are also utilizing a hybrid workforce model, where skilled labor is supplemented by automation and technology. While nothing can replace the expertise of a skilled tradesperson, tools like robotics for repetitive tasks and AI for design and project planning help reduce the pressure on our workforce and increase overall productivity.
6. Managing Costs and Budgets Transparently
Given the price volatility we’ve seen across materials, we are working closely with clients to ensure transparency and communication regarding potential budget adjustments. If costs increase due to material shortages or inflation, we make sure our clients are informed well in advance, and we collaboratively assess how to best manage these changes.
We also focus on building flexibility into our contracts to accommodate market fluctuations, which allows us to keep projects on track even when prices change unexpectedly. Clear communication with clients, suppliers, and our team ensures everyone remains on the same page as we adapt to these challenges.
Looking Forward: The Future of Construction in BC
The construction business in BC has a bright future despite the present difficulties. BC will remain a construction hotspot due to rising investments in public works, real estate, and infrastructure. But as we continue to adjust to the shifting environment, our approach to building projects will probably change.
Innovation in materials, technology, and workforce management will help us build more efficiently and sustainably, even in the face of supply chain disruptions. At our company, we are committed to staying ahead of industry trends and providing the best possible service to our clients, no matter the challenges.
In conclusion, even though BC’s construction industry faces serious supply chain challenges, the industry’s adaptability and tenacity guarantee that we will continue to produce high-quality projects. By using technology, maintaining flexibility, and cultivating closer ties with supplier. We are certain that project planning will enable us to satisfy the needs of a constantly changing market and uphold our standing as an industry leader.