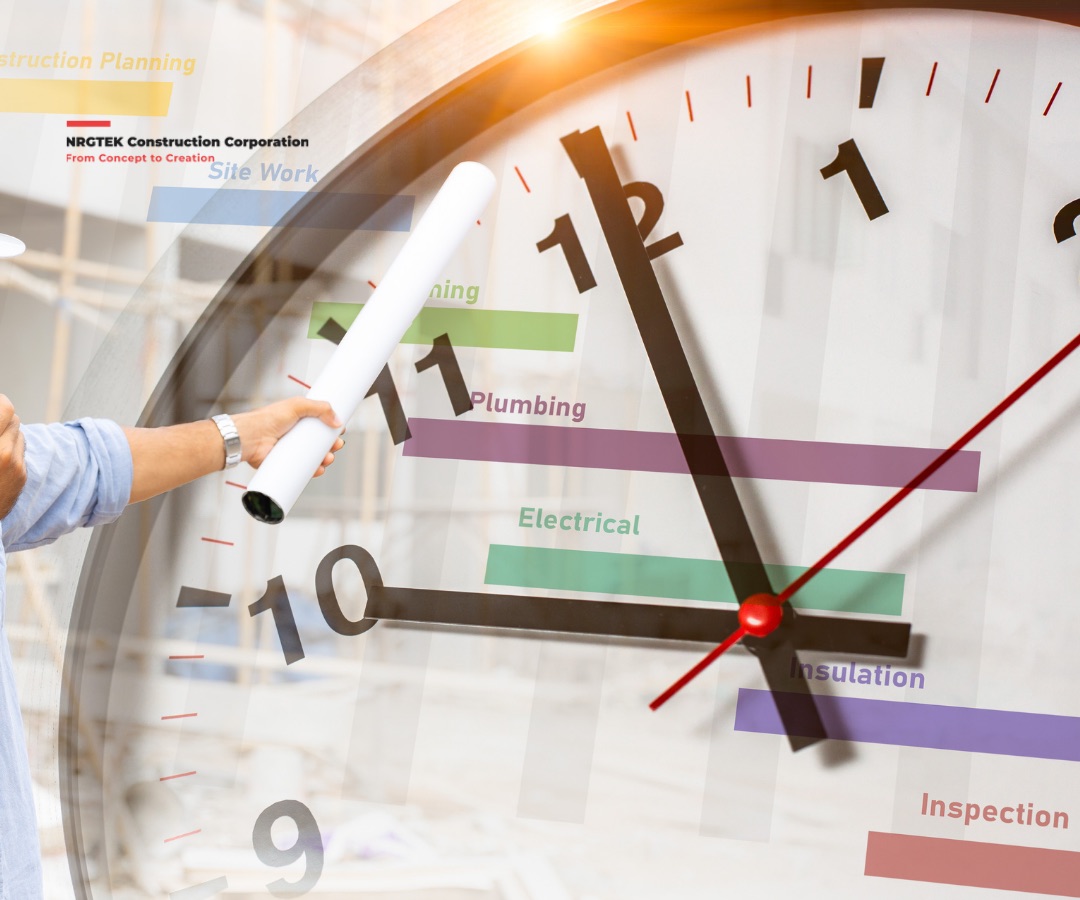
The process of creating a custom home is thrilling and gives homeowners the chance to create a space that suits their unique requirements and preferences. But building a custom home is a complicated process with many moving parts that can affect how long the project takes. Whether you’re building your ideal home in British Columbia or somewhere else, being aware of the possible delays will help you plan ahead and control your expectations. Here are a few typical causes of delays in the schedules for building custom homes.
1. Permit Delays
The permit approval procedure is one of the most frequent reasons for construction delays. Before construction can start in British Columbia, homeowners must obtain a number of permits, such as zoning approvals, building permits, and environmental assessments. This process may take weeks or months, depending on the municipality and the intricacy of your project. Inconsistencies in the application, missing supporting documentation, or the need for additional agency approvals could all cause delays.
How to Avoid This: Get the permitting process started as soon as possible and collaborate with seasoned architects or contractors who are knowledgeable about local laws and can guide you through the system effectively.
2. Weather Conditions
Weather is a major factor in construction delays in places like British Columbia where the weather can be erratic, particularly during the rainy season. Everything from excavation to concrete curing can be impacted by rain, snow, and extremely cold temperatures. Project delays may result from heavy rainfall, which is typical in coastal areas and can make certain tasks impossible, such as pouring foundations or framing.
How to Avoid This: Consider the local climate when planning your construction schedule. Even though you have no control over the weather, it can be helpful to plan important outdoor tasks for the drier months and allow for weather-related delays in the schedule.
3. Supply Chain Disruptions
The timeline for your custom home may be impacted by the supply and material availability. Transportation delays, material shortages, and global economic factors have all contributed to an increase in supply chain disruptions. Particularly if you are sourcing custom or imported materials, items such as windows, steel, lumber, and specialty fixtures may be delayed. While waiting for essential components to arrive, a lack of materials can cause the project to come to a complete stop.
How to Avoid This: Select easily accessible materials or talk to your contractor about non-delays alternatives. Additionally, to account for longer lead times, place your order for custom materials early on.
4. Changes to the Design or Scope
During the building process, homeowners frequently ask for design modifications or add new features to their custom home. Although these modifications are reasonable, they frequently cause delays because they may call for new plans, more permits, or material reorders. Even small changes have the potential to throw off the project’s timeline by days or even weeks.
How to Avoid This: Complete all design choices prior to the start of construction and adhere as closely as you can to the original plan. If adjustments are required, talk about them with your builder as soon as possible to determine how they will affect the budget and schedule.
5. Site Issues
Unexpected delays in the construction of custom homes can result from problems with the building site. These problems could be anything from challenging soil conditions that call for more grading or excavation to finding unanticipated underground water or rock formations. Site difficulties are frequently unanticipated and can have a big influence on the schedule, especially in the beginning phases of the project.
How to Avoid This: Before beginning construction, perform a comprehensive site inspection that includes geotechnical evaluations. This enables you to make appropriate plans and helps detect any possible issues early on.
6. Subcontractor Scheduling Conflicts
A custom home requires a variety of trades and subcontractors, including painters, roofers, plumbers, and electricians. Their schedules can be difficult to coordinate, and if one part of the project is delayed, it can affect the rest of the project. The project may stall until a subcontractor is available if they have overbooked their time or are unavailable when needed.
How to Avoid This: Assist a seasoned general contractor who has built trusting connections with trustworthy subcontractors. All trades can be made available when needed with the aid of effective project management and scheduling.
7. Inspections and Compliance
Inspections are necessary at different points during the building process to make sure that building codes and regulations are being followed. If an inspection is unsuccessful or the local building authority is slow to schedule inspections because of high demand, delays may result. The timeline might be delayed each time an inspection needs to be rescheduled or remedial work is needed.
How to Avoid This: Make sure your builder is knowledgeable about the local building codes and is doing work that complies with or surpasses them right away. Delays can also be avoided by scheduling inspections as early as possible.
8. Financing and Payment Issues
Financing delays may cause your custom home’s construction to stall or even slow down. Late payments, modifications to the loan terms, or unforeseen expenses that surpass your budget can all cause problems. As construction teams wait for payments before placing material orders or making payments to subcontractors, these financial setbacks may cause delays.
How to Avoid This: Work with your contractor to create a clear payment schedule and secure funding well in advance. Maintaining a contingency in your budget to deal with unexpected expenses will also help you stay on schedule.
9. Labor Shortages
The construction industry frequently faces a shortage of skilled workers, especially in crowded markets like British Columbia where there may be a greater demand for new homes than there is labor. Your project may be delayed by a lack of skilled craftspeople, particularly during the busiest building seasons.
How to Avoid This: Start your project in the off-peak months when labor might be easier to come by, or choose a contractor with a solid track record.
10. Unforeseen Circumstances
Unexpected construction delays may result from unforeseen circumstances like natural disasters, political upheavals, or even worldwide occurrences like pandemics. Even though they are uncommon, these significant disruptions can affect everything from labor availability to material availability, making it challenging to forecast with precision when a project will be finished.
How to Avoid This: Unexpected events cannot be avoided, but you can manage them if they do occur by being flexible with your timeline and keeping lines of communication open with your builder.
Conclusion
The process of building a custom home is both thrilling and complicated, and being aware of the possible setbacks will help you control your expectations. Certain delays, such as those caused by inclement weather or site conditions, are out of your control, but others can be reduced with careful preparation, open communication, and collaboration with knowledgeable experts. You can keep your custom home project as close to schedule as possible and enjoy your new space with fewer headaches along the way by foreseeing these potential obstacles and remaining adaptable.